Manpower & Talent Retention
Treating employees as the partner of co-prosperity and co-existence, we value employee diversity and equal opportunity and hire international migrant workers, indigenous peoples, and persons with disabilities as one of us. To improve the harmonious relationship with local communities and employee retention, we prioritize employment for residents of local communities.
To make happy workplace a reality, apart from establishing the breastfeeding (lactation) room, we also provide the unpaid parental leave plan by law for qualified employees to take parental leave. (Please refer to our Sustainable Report for statistics)
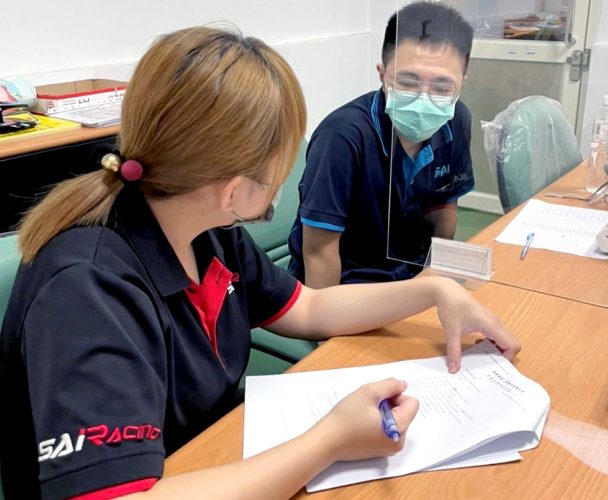
Human Rights & Employee Benefits
Contributions to the Labor Retirement Reserve Fund in accordance with the Labor Standards Act. In accordance with the Labor Standards Act, the pension is calculated based on the service length (seniority) and the average wage of employees in the past six months before retirement. Each month we contribute 2% of the employee’s total amount salary to the Labor Retirement Reserve Fund for the Labor Retirement Reserve Fund Supervisory Committee to deposit the sum in the special account at the Bank of Taiwan in the name of the Committee.
For the pension contributed under the Labor Pension Act, we contribute 6% of the employee’s salary each month to the employee’s personal special account at the Bureau of Labor Standard in accordance with the “Employee Retirement Regulations” established in accordance with the Labor Pension Act.
Our employee benefits are as follows:
- Free health checkup each year and regular in-house physician consultation.
- Cash gifts on birthday and Labor Day, children study grants, childcare benefit.
- Wedding cash gift, funeral cash assistance, birth cash gift, and hospitalization cash assistance
- Travel funding and contract store discounts.
- Activities such as Family Day and year-end reunion.
We value employee opinions and actively hold labor–management meetings and form the staff welfare committee to promote opinion exchange with employees. Each department also holds communication meetings from time to time to cohere consensus through consultation and thereby promote labor–management harmony. We have also set up an employee grievance box for employees to file grievances. We will address employee grievances according to the relevant regulations to protect the rights and interests of employees. We will continue to arrange awareness education of the relevant systems and regulations for employees to understand their own rights and interests and the Company’s handling principles. Additionally, we will publicize to employees and remind them of the relevant information at the executive meetings, enterprise activities, and internal social media.
When terminating an employment contract in accordance with Article 11 or Article 13 of the Labor Standards Act, the minimum notice periods are as follows:
- 10 days in advance for working continuously for over 3 months but less than 1 year.
- 20 days in advance for working continuously for over 1 year but less than 3 years.
- 30 days in advance for working continuously for over 3 years.
After receiving the said notice, employees may apply for leave to find another job during the working hours. The maximum length of “paid job-seeking leave” shall not exceed 2 days of working hours each week. Employers terminating the employment contract without notifying employees according to paragraph 1 shall pay employees the wage of the notice period.
We have been audited for human rights by customers during the reporting period. The rating of both the contents and results is A. Customers provided the Supplier Assurance Questionnaire (SAQ) for suppliers to measure their performance in human rights (working hours and employee wage and benefits), conflicts of interests in employees, supplier management principles, environmental compliance, and similar issues to verify compliance and future planning for implementation.
To enhance the realization of human rights, we arrange courses relating to human rights in new employee training. The training content includes gender mainstreaming, sexual harassment prevention, gender equality, labor laws and regulations, and the Labor Standards Act.
Career Development & Wages
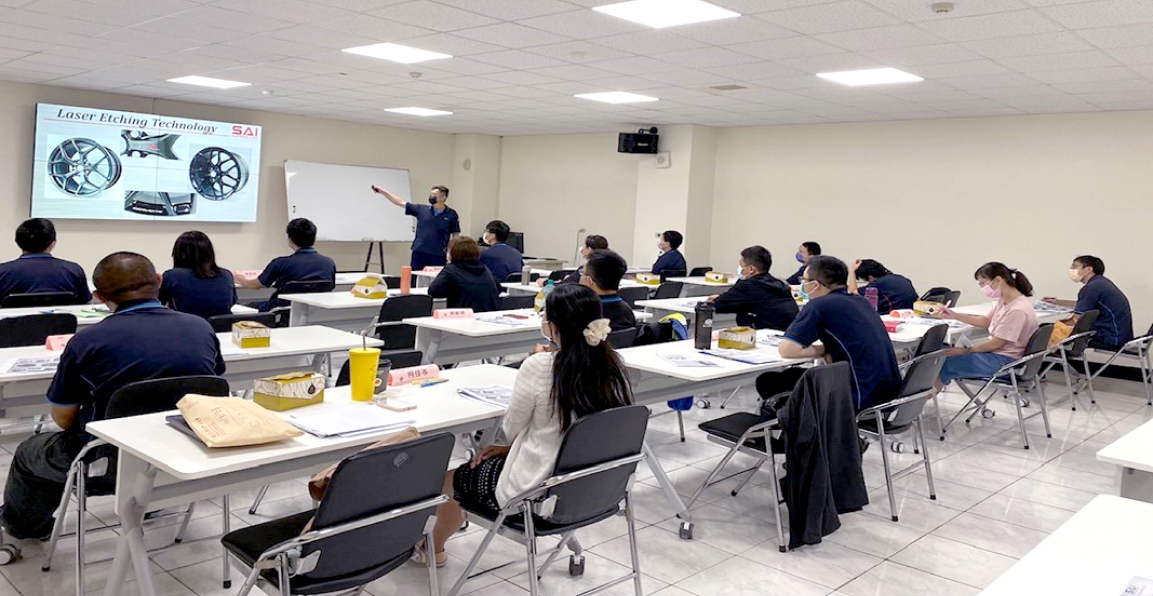
Employee Training Plan
Excellent human resources are the cornerstone of corporate sustainable development. To improve the competency and literacy of employees and maintain long-term competitive strengths, we offer competency learning to employees, including developing the Employee Skill Learning Roadmap, organizing study groups, and arranging staff training courses.
Equality in Performance Evaluation
With quantitative job targets and qualitative competence performance, we fully combine overall corporate operating profit with employee personal performance.
Employee Wages
The wage of base-level employees is the same as the local minimum wage. We endeavor to maintain wage equality, prevent workplace gender discrimination, and ensure wage fairness within the company.
We has become a listed company from 2024, we set OTC trade as our future goal. Hence, apart from following the requirements of the Taiwan Stock Exchange Corporation Rules Governing the Preparation and Filing of Sustainability Reports by TWSE Listed Companies, in the voluntary disclosure of this report, we additionally disclose the wage-related information of employees.
Workplace Safety Management
Apart from implemented the ISO 45001 occupational health and safety (OH&S) management systems, we have also established the ESH manual and various SOPs to enhance corporate competitiveness and effectively reduce work-related hazards. By identifying OH&S risks and making progressive improvement, we aim to lower the impact of work-related hazards on employees and contractors, reduce work-related injury from accidents, enhance OH&S performance, and protect the OH&S of employees. We make four commitments for employees in our OH&S policy:
Promote ESH awareness
Comply with ESH-related laws and regulations
Accomplish ESH targets
Improve ESH in manufacturing processes
Hazard Identification and Risk Assessment Flowchart
Occupational Accident Flowchart
Occupational accidents are divided into two categories: in-house accidents (work-related accidents) and out-house accidents (traffic accidents). We assist employees in applying for occupational accident and work-related in claiming compensations for occupational accidents and work-related injury and disease in accordance with the Occupational Safety and Health Act and the Labor Insurance Act. Immediately after an accident occurs, employees shall voluntarily report to the unit head for the unit to assist in claiming occupational accident insurance. Statutory significant occupational accidents shall be reported within eight hours by law. Then, the HR unit shall assist in claiming compensations for work-related injury or disease under the Labor Insurance so as to optimize the aftercare of employees.
We implement noisy environment monitoring once every six months in workplaces with noise exposure. To prevent hazards, suppliers are requested to maintain the noise of machinery and equipment below 85dB through source control. We also implement hearing health checkup for employees every six months. Engineering improvement is implemented on in-house high-noise machinery by insulating or wrapping up the noise source. Earplugs are replaced with earphones for workers working in special noisy areas.
Dust environments in dusty workplaces are monitored once every six months to understand the actual state of dust exposure of workers for effective control and hazard prevention. Suppliers are requested to add dust guards or local exhaust devices to machinery and equipment to reduce dust production at the source. We also arrange chest X-ray examination for workers every year for prevention.
Employee Health Checkups
To effectively prevent occupational disease and occupational accidents, we implement workplace environmental monitoring, reduce hazard exposures, arrange safety and health education and training, offer periodic health checkups for employees, provide work-based preventive follow-up, and organize employee health promotion activities.
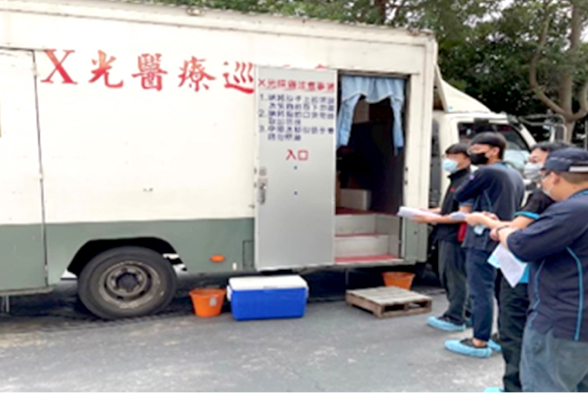
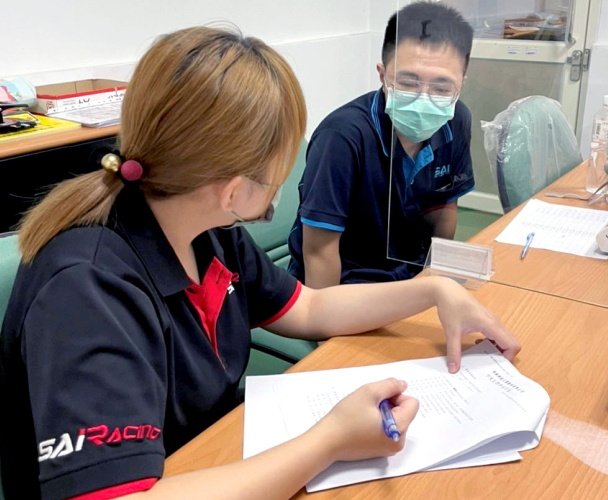
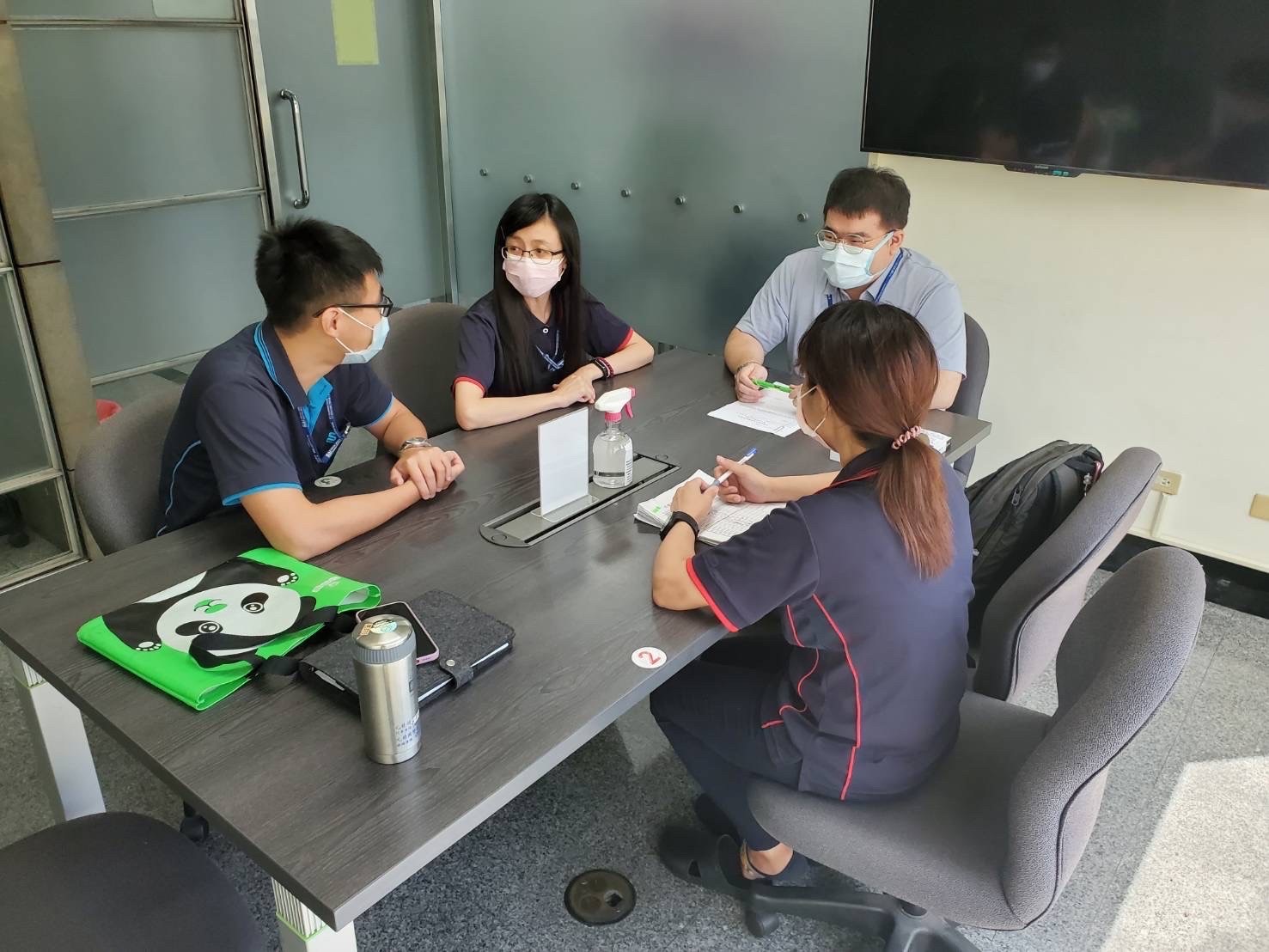
OH&S Committee
We have established the OH&S Committee with members including occupational safety and health management personnel and occupational health management specialists. Members also include members of different areas (technicians, department heads, supervisors, and commanders relating to OH&S) within the plant. Six of them are representatives selected by the labor–management meeting, accounting for a third.
The OH&S Committee holds a committee meeting once each quarter to coordinate and recommend important items in the employee HSE policy and OH&S management plan, review work progress, report on the quarterly EHS results and changes in the external environment, and review the counteraction for the current environmental status, equipment, and operational conditions.
The structure of the OH&S Committee is as follows:
Chairperson
OH&S Committee
Office for Occupational Safety and Health Management
(master OH&S unit)
Occupational Safety and Health
(Plant I, Plant II, Plant H, Chuwei Plant, Pingtung Plant)
Management Performance of OH&S Committee
We have established the Supplier and Contractor OH&S Management Procedures in accordance with ISO 45001. The OH&S management systems apply to all works within SAI workplaces, with 100% coverage. They also apply to the employees of contractors, also with 100% coverage
Suppliers
One audit is arranged. If significant quality or ESH defects are detected, additional audits will be arranged as necessary based on the sales condition.
Contractors
The OH&S unit will arrange irregular OH&S audits on contractors working in-house, record detected anomalies, and issue penalty tickets as necessary.
- The purchasing unit has established the Supplier Audit Control Procedures (DOC-00044403-006) and include ISO 45001 in the management procedure to facilitate supplier audits.
- The purchasing unit draws up the audit schedule of suppliers and contractors and may conduct on-site audits at the premises of suppliers.
- ESH audits will be performed on suppliers and contractors to ensure their ESH compliance.
- When ESH issues are detected in suppliers and contractors, defect investigation and corrective and preventive action review and effectiveness follow-up will be implemented.