Technology
Our technical team is equipped with design, engineering, and manufacturing capabilities accomplishes, allowing us to create SAI forged products using computer-aided design (CAD), computer-aided engineering (CAE), and computer-aided manufacturing (CAM).
Design
The capacity of our technical team includes mold design and manufacture; design, development, flow analysis of forging molds, machining of high-precision products, surface polishing and optimization, and painting. During the design and development phase, finite element analysis is applied to calculate the optimal structure to shorten the design and development lead-time, save costs, and deliver optimal lightweight designs. With capabilities covering 3D design, structural design, high-quality curvature modeling, motion simulation, finite element analysis, reverse engineering, and craft design applicable to the aerospace and automotive industries, we provide bespoke products for customers demanding a streamlined style.
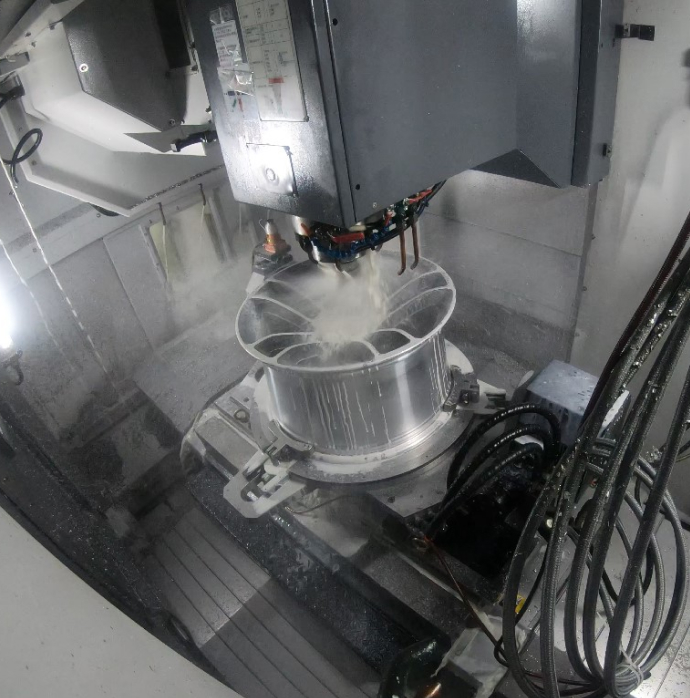
Production
1
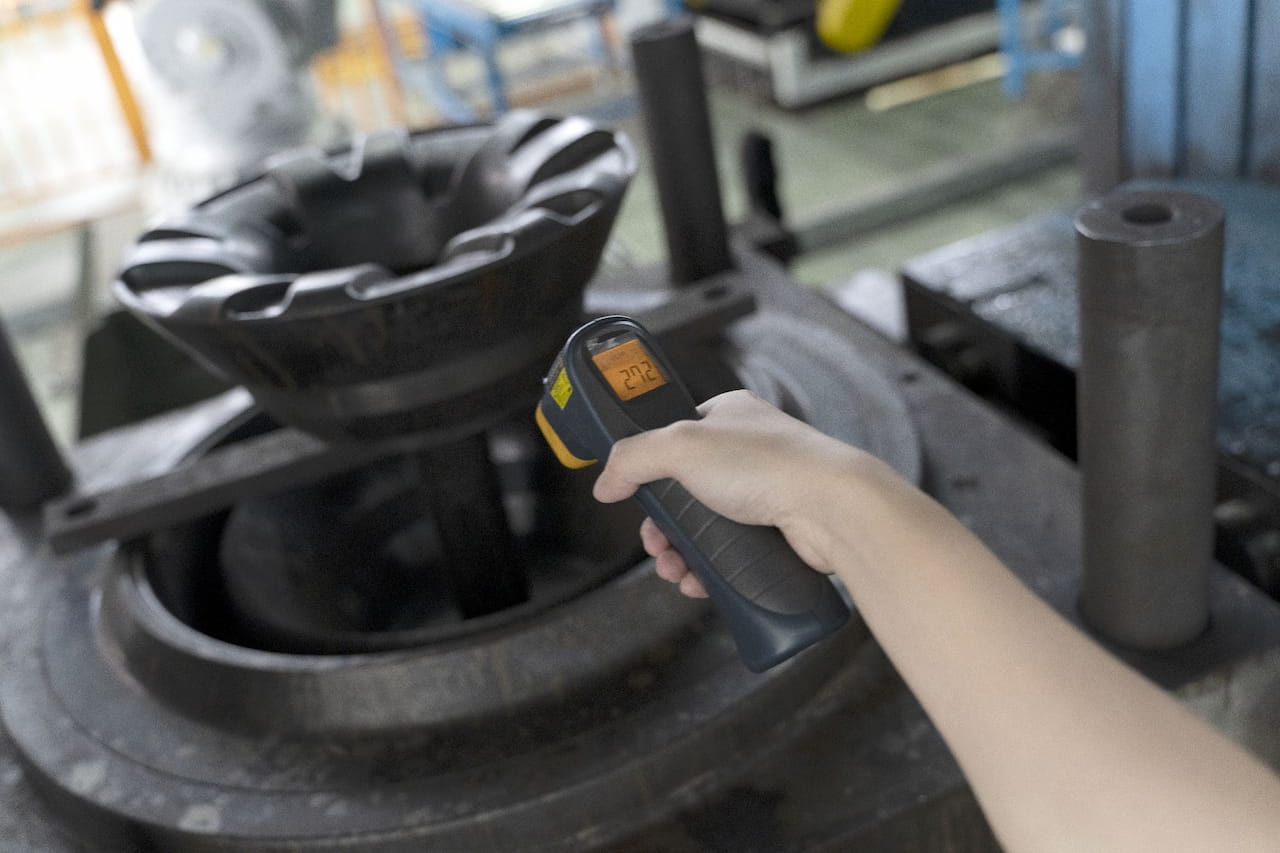
Forging
After crosschecking the simulation results of forging mold flow simulation and analysis with different types of mold flow analysis software, judgement and revision are eventually made based on the forging know-how accumulated over the years to prevent potential defects and search for the optimal process condition and design.
2
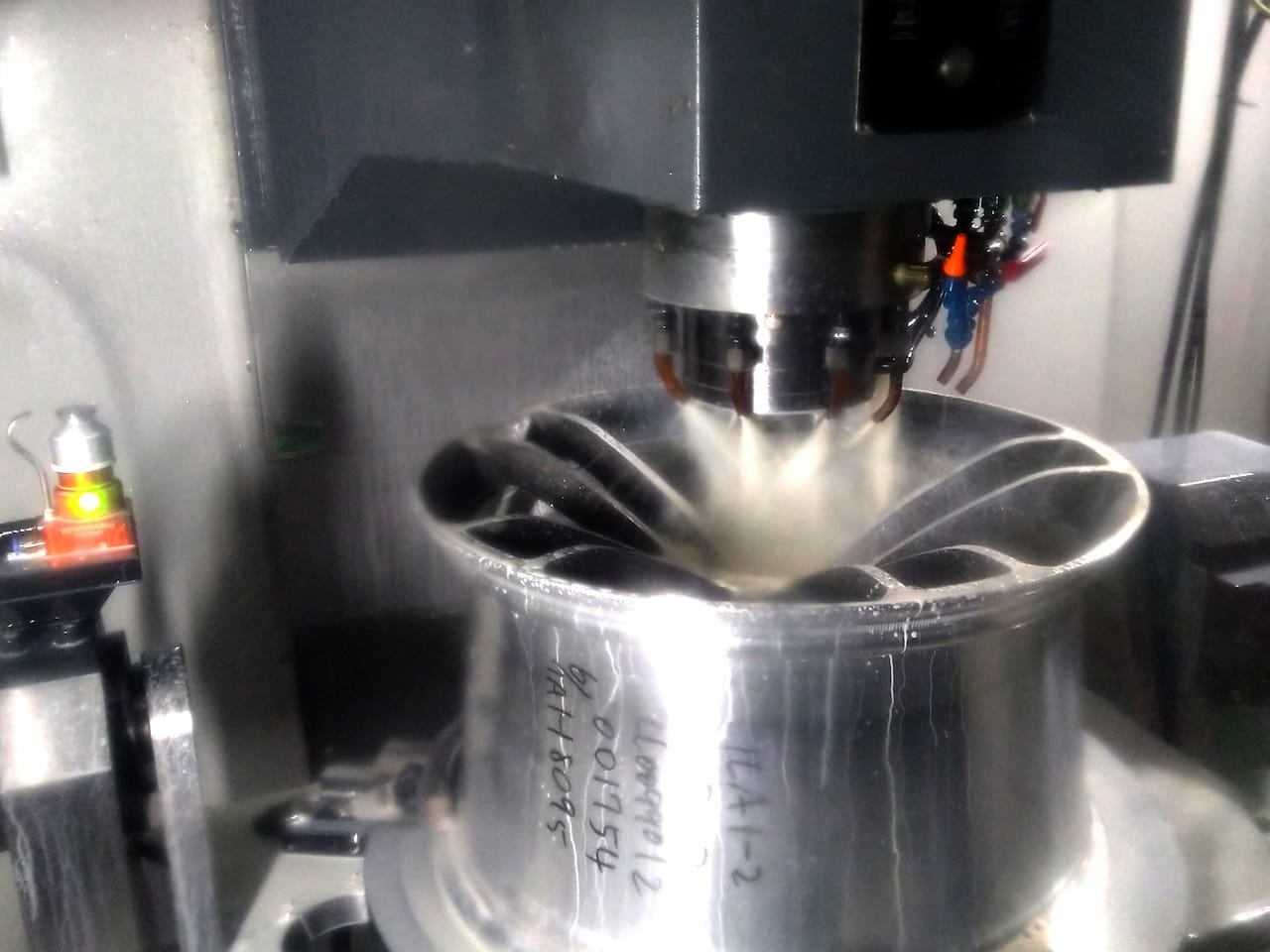
Machining
In response to customer demands for diversity, low volume, high-precision, and complex curvature, we write machining programs with advanced CAM to integrate high precision with high-quality curvature 3D to produce products with optimal surface precision and assembly.
3
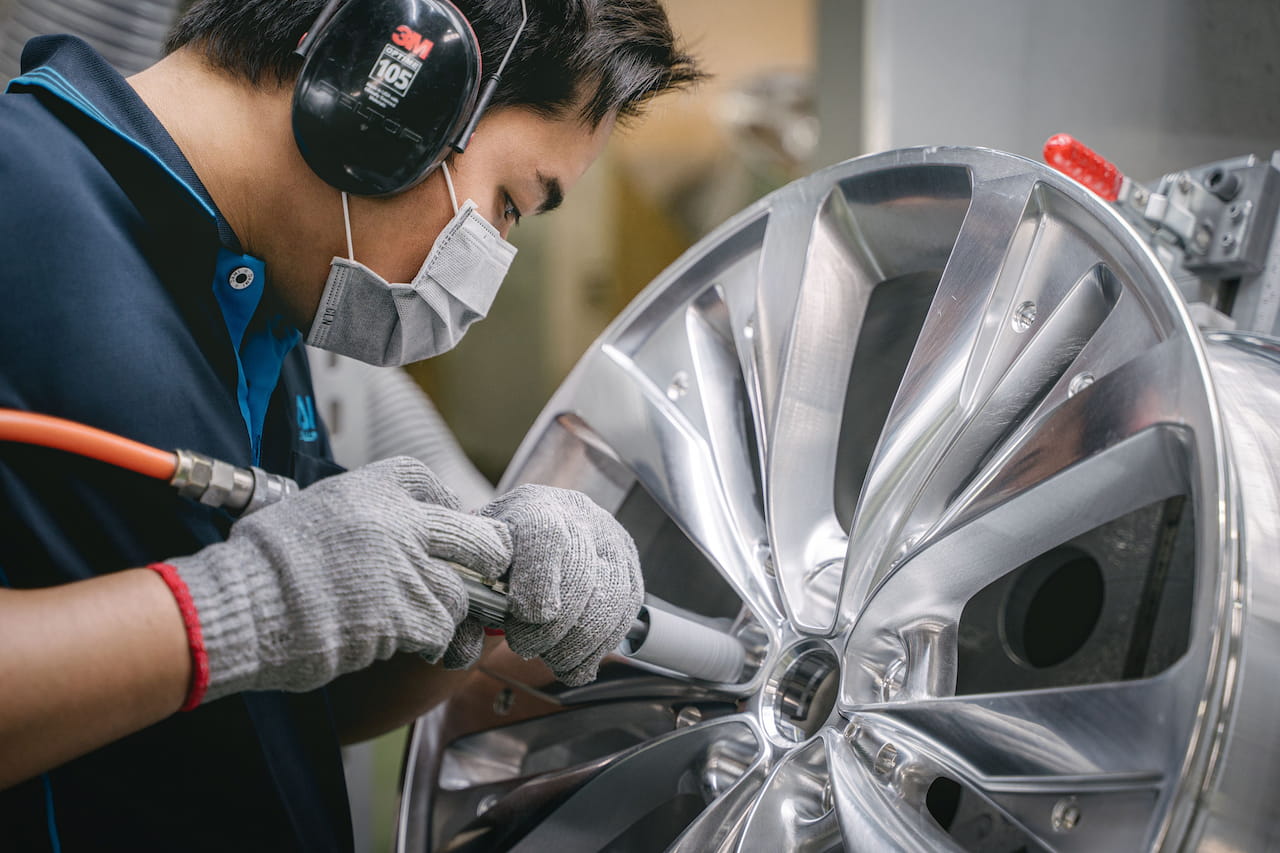
Polishing
Professional technology and equipment are used in polishing for surface optimization. Mechanical polishing, dynamic polishing, and ceramic polishing techniques are applied to present the natural luster and color of forged aluminum according to the appearance requirements of customers.
4
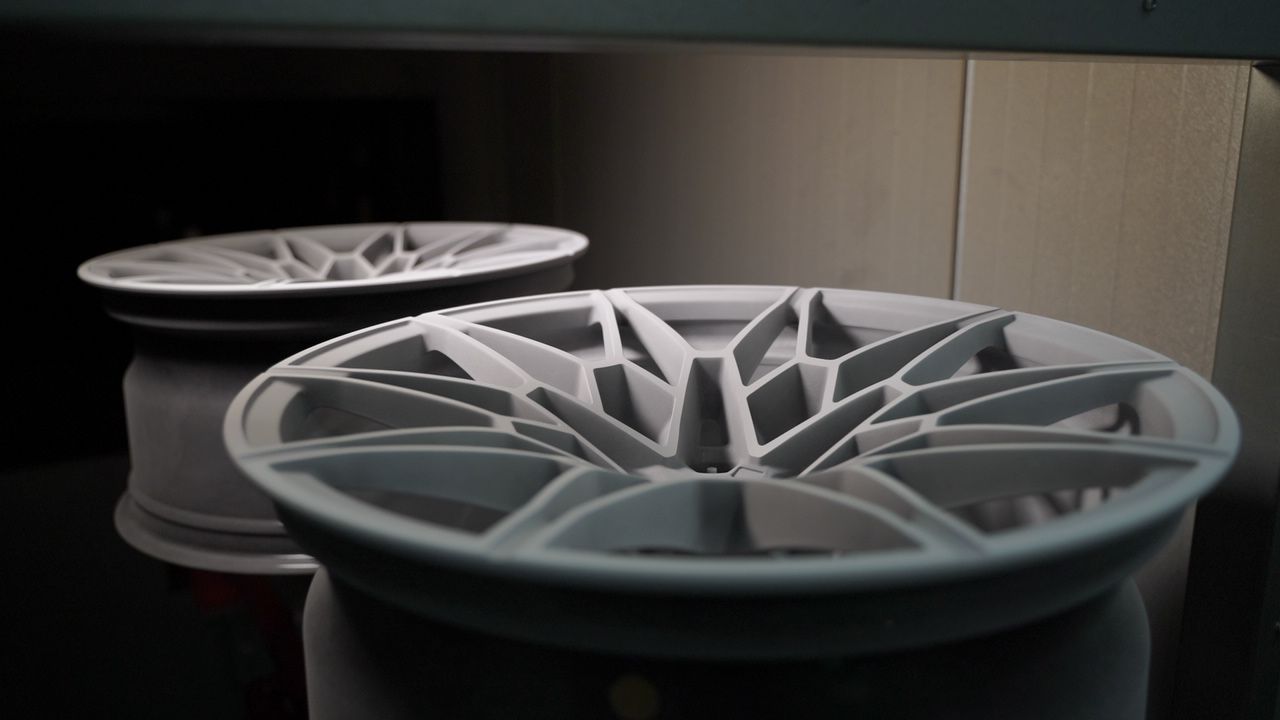
Painting
Robotic arms are equipped on the entire painting line to meet different paint and luster requirements and control appearance quality through automation. Since products are getting increasingly complex nowadays, we fulfill the diversified demands of our customers with masking, machining, laser engraving, pad printing, and HRNT.
Forging Process
SAI’s main product is forged aluminum alloy wheels. We have two different manufacturing processes to meet all kinds of customer needs.
CNC forging can maintain high design freedom, while net shape forging can save the complex and long cycle time of machining for mass production.
CNC Forging
Net Shape Forging
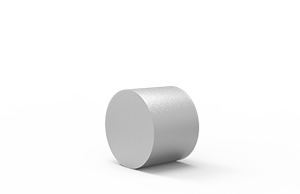
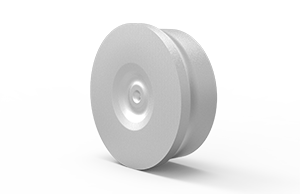
Pre-forging
Materials consumption and allocation are determined based on the style and structural demands of customers. Primary forging press delivers high contour stability, with high design freedom provided by a multiple machining process.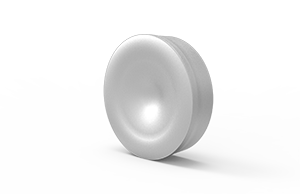
Pre-forging
Materials consumption and allocation are determined based on the style and structural demands of our customers.
Rough forging
Form the rough shape and optimize materials allocation between pre-forging and fine forging.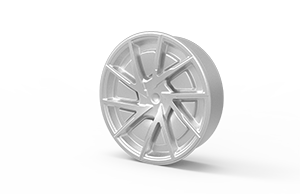
Fine forging
Directly form the design surface according to the style and flow-forming requirements of customers. Optimize fatigue performance through grain flow design. Save the expensive cost of machining cycle time with outstanding forging technology. Suitable for mass production to address the requirements of increasingly tightening energy and emission reduction requirements.
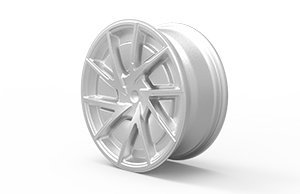
Appearance

Fully Painted
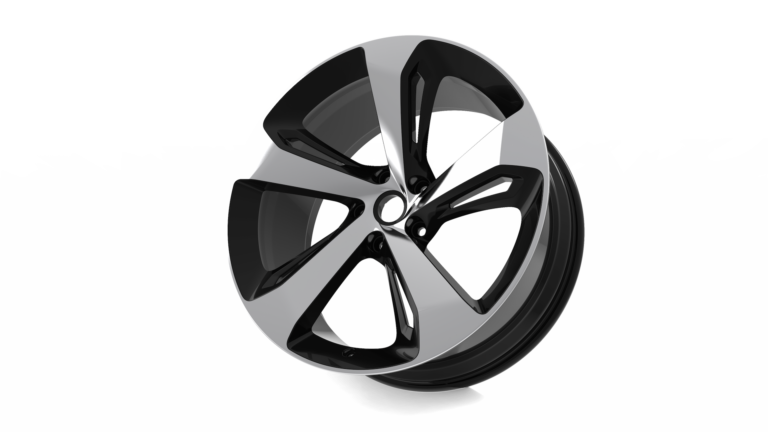
Bicolored – Natural aluminum color + selected color
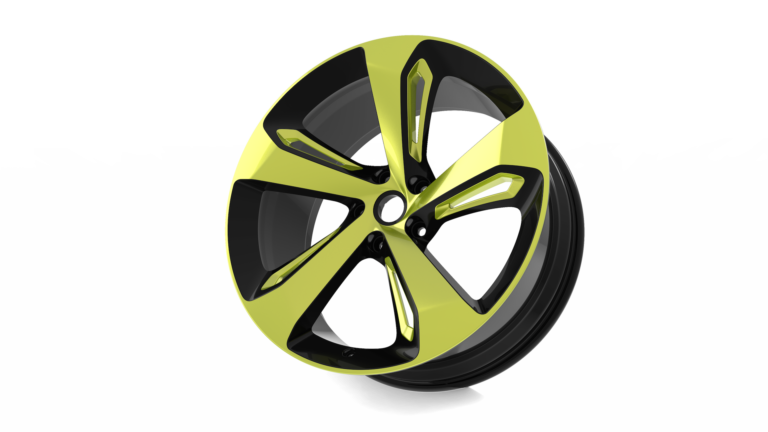
Bicolored – Two selected colors
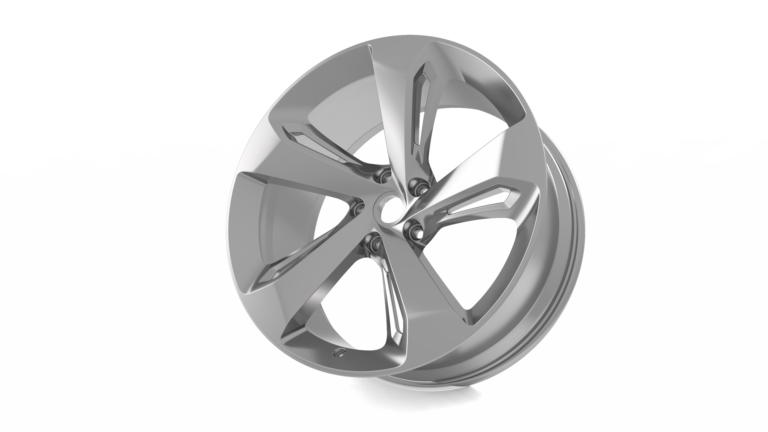
Ceramic Polish
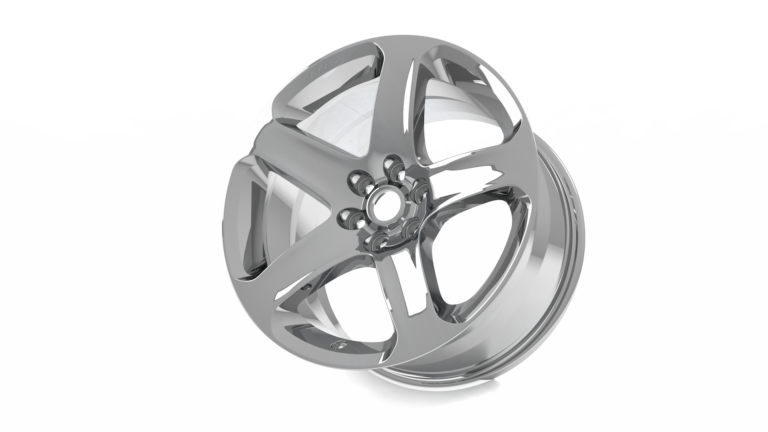
Mirror Polish
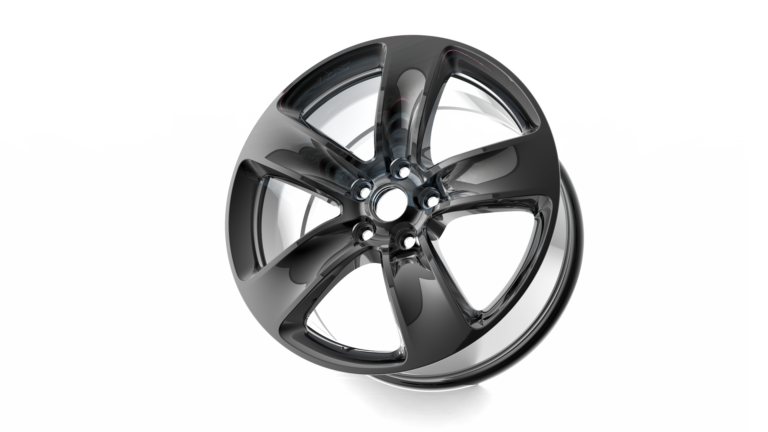
PVD Vaccum plating (Sputerring)
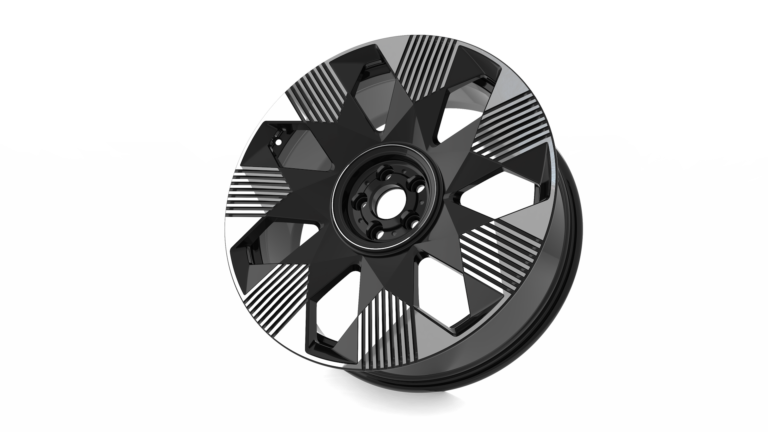
Multilayer painting with lathing and milling
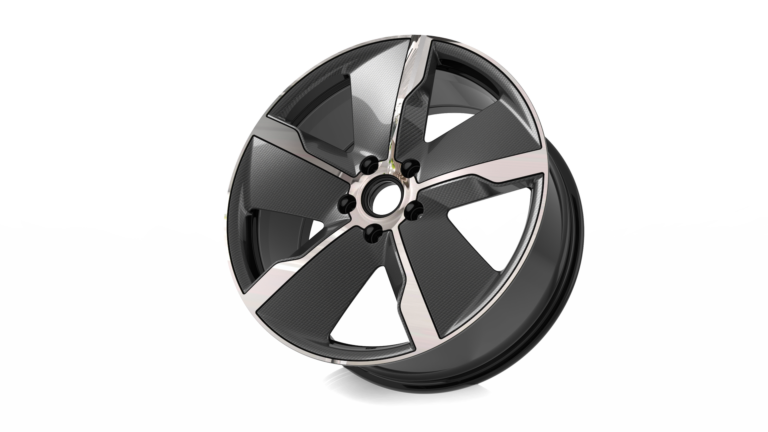
Accessories
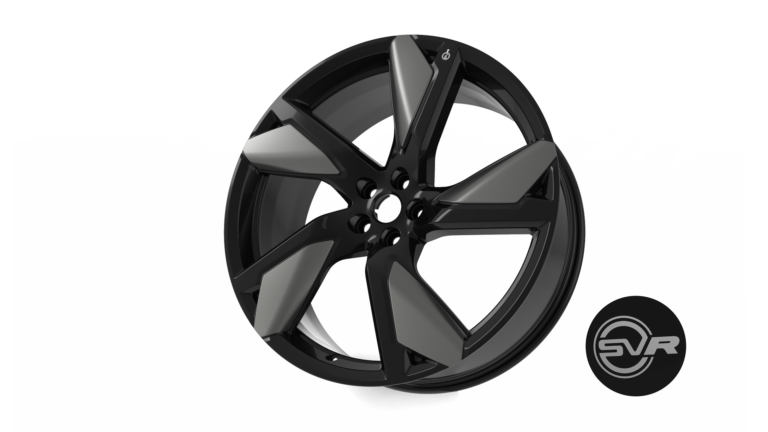